“The combination of digital and industrial capabilities creates value”
For Sébastien Condom, General Manager Digital Turbomachinery Solutions at GE Oil & Gas, the ability to collect and process data, especially from project design, will improve the productivity of operations, for example through process optimization. and reducing plant downtime. “We are on the cusp of an in-depth change in the O & G sector,” he said, also referring to GE’s launch of the Predix platform, dedicated to the industrial Internet, or the concept of ” digital twin”.
PGI: What is the scope of GE Oil & Gas’s business?
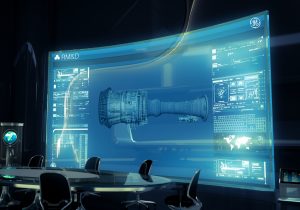
Sébastien Condom: GE Oil & Gas is a General Electric Group company present throughout the value chain of the sector, from the wellhead to the refinery, through the underwater production systems, the machines petrochemicals, LNG, transport and storage. Our entity employs 37,000 people and achieved a turnover of $ 16.5 billion in 2015. Our ambition is to invent the next industrial era in the field of O & G and push the frontiers of technology to solve the most difficult problems in the sector. GE Oil & Gas has the knowledge and technical expertise that combine the physical world and the digital world. We think this is the equation of success for the future.
PGI: At the moment, the O & G industry is evolving in the context of low oil prices and cost reduction plans initiated by prime contractors …
SC : Current times call for more collaboration and proximity between different market players. Better ecosystem optimization will inevitably lead to cost reductions that will allow more sustainability over time for our industry. These times also call for more co-creation of solutions. We are currently working with BP, in the Gulf of Mexico, on a digital project whose goal is to reduce the downtime of an offshore installation. Finally, these complicated times call for an even greater search for productivity. Operational inefficiency figures are particularly significant. The non-operability of a well can cause up to $ 3 million in lost revenue per week,
PGI: What is GE’s vision for digitizing the O & G sector?
SC: We believe that in the O & G sector, the combination of digital and industrial capabilities creates value because it meets the specific needs of this industry, especially to address the quest for productivity that is needed today in the world of energy. It is estimated that an increase of
1% of the availability rate of production systems has an impact of $ 5 to $ 7 billion on the activity of our industry. In the same vein, a 1% increase in the oil recovery rate, which currently stands at 35%, is equivalent to three years of production, which represents 80 billion barrels. In the O & G industries, a small increase in productivity has potentially massive effects. And this, especially as we still have little, if any, exploited the potential of the use of data.
PGI: Yet, in the O & G industry, has process data collection been a reality for a long time?
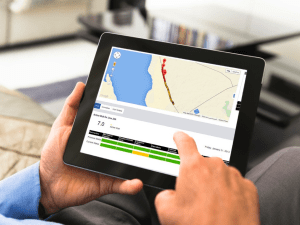
SC: That’s right, but on a standard installation, only 15% of sensors are used for decision support and therefore for optimization. If the O & G industries are already acquiring a lot of data, the challenge today is how best to use this phenomenal amount of information. We calculated that GE’s only fleet of rotating machines produces 500 terabytes of data every day, more than any Facebook user in the world. Today, there are more than 100,000 critical rotating machines in operation worldwide, millions of kilometers of pipeline and millions of submerged electric pumps …
If we begin to consolidate the data from all these equipment and materials, use them and apply analytics that will lead to more productivity, we are really on the cusp of a change in depth of the O & G sector. In addition, we have access today to a new optimization potential that is linked to the new capabilities of digital. Thus, we have more possibilities to connect equipment at a low cost, and thus to collect data that was until now only available on site. We also have more computing capabilities and therefore the ability to do analysis, apply statistics to these data and make data science .
PGI: GE has opened this year the Predix platform dedicated to the industrial Internet. What is his vocation?
SC:Our Predix platform, which is both an infrastructure and a development environment, is the only Cloud (1) platform designed for the needs of the industry. It therefore has the ability to ingest masses of data and easily apply a number of analytical tools that can be developed by different users for productivity purposes. Predix is an open source operating system (OS) that supports applications developed by GE as well as third parties: operators, EPCs, system integrators, suppliers or OEMs (2). Our customers, our partners and our competitors can develop on Predix. It’s a real ecosystem. The objective of this platform is to serve the entire value chain in a transversal and open way, but, of course, Predix users keep ownership of their data. As for the applications developed, they can be marketed directly by their developers. The subjects possibly treated by Predix are infinite. Thus, we are currently developing, on this platform, an Asset Performance Management (APM) solution that integrates features of Smart Signal (3), one of our APM applications that allows, by identifying parameter deviations from to a model, to predict a slow evolution of these parameters and thus to make predictive maintenance.
PGI: Last June, you signed a memorandum of understanding with Technip to develop digital solutions in the field of LNG. What are the objectives?
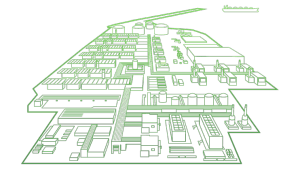
SC:This non-exclusive agreement with Technip, a long-standing GE partner, aims to identify opportunities for optimizing the LNG value chain. It’s not just a question of applying Big Data solutions to already running installations, but also to ascertaining the value chain and determining the optimization possibilities that can, from the design stage, make an installation more efficient. The challenge is to determine where, in an LNG project, the potential sources of productivity are by setting goals that could be, for example, a 15% reduction in commissioning time or 20% of maintenance costs, or still a 2% increase in the availability of a liquefaction plant. This type of collaboration is transferable in many other sectors of the industry, for example FPSOs and offshore. It is an ambitious project but the combination of our digital solutions and our physical expertise creates new and strong potentials.
PGI: Can you give us a concrete example?
SC: By working upstream in the engineering chain, you can begin to collect a variety of data, such as engineering models, inspection data, and test data, and build what you call the “Digital twin”, or digital twinequipment, assembly or complete plant. You can follow the life of this equipment, from the design to its dismantling, estimate its remaining life, the maintenance work to be done, make the prediction … This possibility is based on the ability that Today we have to aggregate data and link them to physical expertise, modeling expertise and engineering. This concept of digital twinis revolutionary and unique. At GE, we are already modeling, on this principle, a number of our equipment, for example rotating machines. More generally, any type of data, whether real-time or discrete, can be processed in a Cloud environment such as Predix. For example, the application of analytics combined with inspection systems can produce new capabilities for predicting defects and anomalies that could generate, almost automatically, advice and recommendations for assisting decision.
PGI: Can you tell us about the digital project you are doing with BP?
SC:We have two ongoing partnerships with BP. The first, which involves connecting approximately 4,000 E & P wells in the coming years, aims to provide BP with an environment that will enable it to implement analytics, statistical algorithms and visualization systems. to optimize processes, especially for what happens inside the wells. The second project concerns a digital co-creation program aimed at optimizing processing topsides on offshore platforms located in the Gulf of Mexico. The goal is to reduce the downtime of these installations by integrating remote control, analytics, and algorithmic solutions across the entire system that include rotating GE machines as well as other suppliers. It is not a question of looking at the performance of only the rotating machines but that of the whole system. This will enable onshore process engineers to more effectively advise offshore teams and guide them on decisions to avoid a shutdown.
(1) Predix is available as a Platform as a service (Paas)
(2) Original Equipment Manufacturer
(3) Read about the predictive maintenance solution for a rotating machinery fleet of Total E & P, published in number 1834 of PGI (January / February 2015).
A breakthrough for the LNG industry
“We are entering into this partnership with the same pioneering spirit that drove us 50 years ago when Technip built the first LNG plant in the world,” says Nello Uccelletti, President. Onshore Offshore, Technip, quoted in a statement released June 14.“Together with GE Oil & Gas, we want to develop digital solutions that create value throughout the life of a project. This partnership is the result of Technip’s unwavering commitment to innovation and technology, which are at the heart of optimizing oil and gas developments. As we did 50 years ago, and as we currently do in the FLNG sector, we are confident that this partnership will be a breakthrough for the LNG industry.”